In the global chemical and liquid logistics industries, Intermediate Bulk Containers (IBC Totes) have become the gold standard for transporting liquids, chemicals, and food-grade substances due to their efficiency, safety, and cost-effectiveness.
With a decade of expertise in plastic product trading and bulk container solutions, this guide provides an in-depth analysis of IBC totes’ advantages, industry applications, and international shipping protocols. By the end, you’ll gain actionable insights to reduce cross-border logistics costs by 30%+ while ensuring compliance and operational excellence.
1. Technical Breakdown of IBC Totes
1.1 Definition & Structural Design
IBC totes feature a triple-layer composite structure, ensuring durability, leak prevention, and compliance with hazardous material transport regulations:
- Outer Frame: Galvanized steel or high-density polyethylene (HDPE) grid (impact resistance ≥10 kJ/m²).
- Inner Container: Food-grade HDPE (2.5–3.5 mm thickness, FDA 21 CFR certified, resistant to chemical corrosion).
- Base Pallet: Modular design (static load capacity ≥1500 kg; dynamic load ≥1000 kg) for easy handling and stacking.
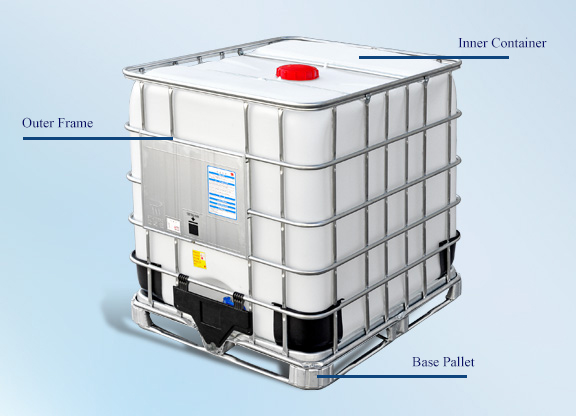
1.2 Technical Specifications Comparison
Parameter | Standard | Anti-Static | Chemical-Grade |
Capacity | 1,000 L | 1,000 L | 1,000 L |
Temp. Range | -40°C to 60°C | -30°C to 50°C | -20°C to 70°C |
Valve Type | Butterfly | Ball valve + grounding | 316 stainless steel |
UN Certification | UN31HA1/Y | UN31HA2/Y | UN31HA1/X |
1.3 Innovative Technologies
- Multi-Layer Coextrusion: Three-layer HDPE inner liners improve oxygen barrier efficiency by 40%.
- Smart Monitoring: Optional RFID temperature sensors (±0.5°C accuracy) for precise tracking.
- Quick-Clean Design: 135° discharge port reduces residue to <0.1% for efficient product turnover.
2. Industry Applications & Case Studies
2.1 Chemical Industry Solutions
- Hazardous Material Transport: Fully compliant with ADR/RID for Class II dangerous goods (e.g., UN 1203 diesel, ethanol, acetone).
- Case Study: A global paint and coatings manufacturer reduced annual transport losses from 2.3% to 0.7% using anti-static IBC totes for flammable liquids.
2.2 Food-Grade Applications
- Aseptic Filling: CIP (Clean-in-Place) systems meet ISO 22000 microbial safety standards for dairy, juice, and edible oil transport.
- FDA & EU Compliance: Ensuring safe handling of consumable liquids without contamination risks.
2.3 Pharmaceutical Compliance
- GMP Standards: Inner surface roughness ≤0.8μm (USP <88> Class VI compliant) to prevent microbial contamination.
- Temp. Control: Phase Change Material (PCM) insulation maintains ±2°C for 72 hours, ensuring vaccine and API (Active Pharmaceutical Ingredient) integrity.
3. Maritime Shipping Protocols
3.1 Pre-Shipment Checklist
- Documentation:
- Valid UN Performance Test Report (5-year validity).
- Material Safety Data Sheet (MSDS) for regulated liquids.
- CTU Code-compliant container certificate.
- Pre-Treatment:
- Cleaning: Residuals <10 ppm.
- Drying: Internal humidity <15% RH.
- Leak Test: 0.3 bar pressure held for 30 minutes to verify seal integrity.
3.2 Container Loading Optimization
IBC Tote Container Loading |
20'GP |
40'HQ |
Units/Layer |
20 |
42 |
Stacking |
2 layers |
3 layers |
Securing |
Cross straps + anti-slip mats |
Honeycomb pads + airbags |
3.3 Risk Mitigation Strategies
- Temperature Monitoring: Refrigerated containers must maintain -5°C to 25°C (±3°C/24h) for sensitive cargo.
- Moisture Control: Silica gel desiccants (≥200 g/m³) protect against humidity-related spoilage.
- Emergency Kits: Include polymer sealants, repair tapes, and spill containment gear.
4. IBC Totes Sea Freight FAQs
Q1: When is UN certification required for IBC totes?
- UN-marked totes are mandatory for IMDG Code-regulated hazardous materials, requiring Packaging Group II standards (≤3.0 bar hydraulic test).
Q2: How to minimize cargo damage claims during shipping?
- Ensure loading density ≥650 kg/m³ to prevent movement.
- Use anti-slip pallets (friction coefficient ≥0.6).
- Layer EPE cushioning between stacks for added protection.
Q3: Guidelines for reusing IBC totes?
- Track cleaning cycles for regulatory compliance.
- Inspect wall thickness regularly (minimum ≥1.2 mm).
- Retire units after 5 years or 10 cycles to ensure structural integrity.
5. Market Trends & Future Outlook
5.1 Technological Advancements
- Smart Totes: GPS tracking + real-time sensors (5-minute updates) improve supply chain visibility.
- Eco-Materials: Bio-based HDPE (60% lower carbon footprint) supports sustainable packaging solutions.
- Modular Systems: Quick-assembly designs triple turnaround efficiency in chemical, food, and pharmaceutical logistics.
5.2 Market Forecast (Grand View Research)
- Global IBC market CAGR: 5.7% (2023–2030).
- Asia-Pacific to dominate with 45%+ market share, driven by China, India, and Southeast Asia's manufacturing boom.
Conclusion: Transform Your Supply Chain with IBC Totes
Adopting high-quality IBC tote solutions delivers:
✅ 20–35% lower logistics costs
✅ 50%+ fewer cargo claims
✅ 80% faster cross-border operations
Contact us today for a customized IBC tote solution, international bulk shipping consultation, and free risk assessment!